Health and Safety
GWA's focus remains on ensuring that we provide a safe workplace for our employees, contractors, visitors and customers, while driving a positive safety culture and actively reducing and mitigating risk.
"We care for each other" is a Cultural Pillar of the organisation that drives our objective to ensure everyone is safe, every day. Supported by the GWA Board and Executive Leadership Team, the GWA Work Health and Safety (WHS) team partner with the business to ensure that operating safely is how we do business every day and in every way.
GWA is committed to maintaining a positive safety culture and a proactive approach to identifying and mitigating safety risks. Workplace safety remains an ongoing focus for the Board and the group Executives.
Highlights through FY23 include:
- The development and implementation of a refreshed 3-year Work Health and Safety (WHS) Strategy focusing on all geographic and functional areas of the business,
- Significant improvements in safety capability with highly skilled and committed WHS resources and investment in safety leadership development,
- Improvement in reporting across the group more than doubling our leading indicator – Worker Insight Frequency Rate in FY23,
- A refreshed WHS risk profile with risk action plans in development to further reduce overall WHS risk,
- Strong focus on understanding psychosocial risk and implementation of well-being programs, and
- Successful external assurance program with retention of ISO 45001:2018 certification for our Australian, New Zealand and UK operations.
Safety Performance Indicators
GWA measures a range of safety performance indicators to provide insight and drive action to reduce WHS risk. We continuously identify, implement, and monitor our activities to ensure we eliminate unsafe acts and practices.
Lead Indicators
During FY23, GWA introduced a new lead indicator – Worker Insight Frequency Rate (WIFR) and more than doubled our reporting through the period following a campaign to encourage reporting and shared communication on our worker’s safety experiences.
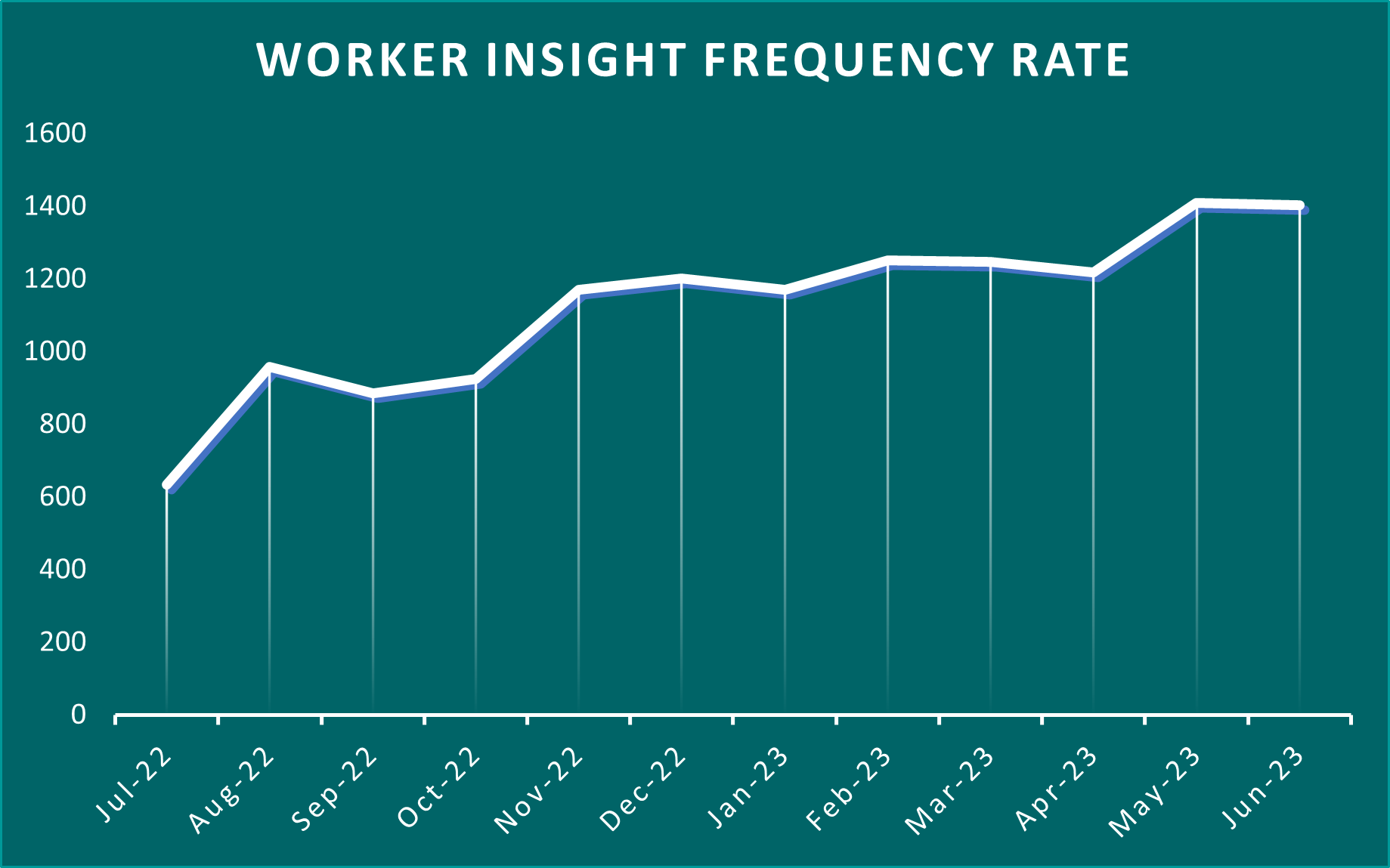
Lag Indicators
GWA continues to measure Total Injury Frequency Rate. During FY23, GWA’s Total Injury Frequency Rate is detailed below:
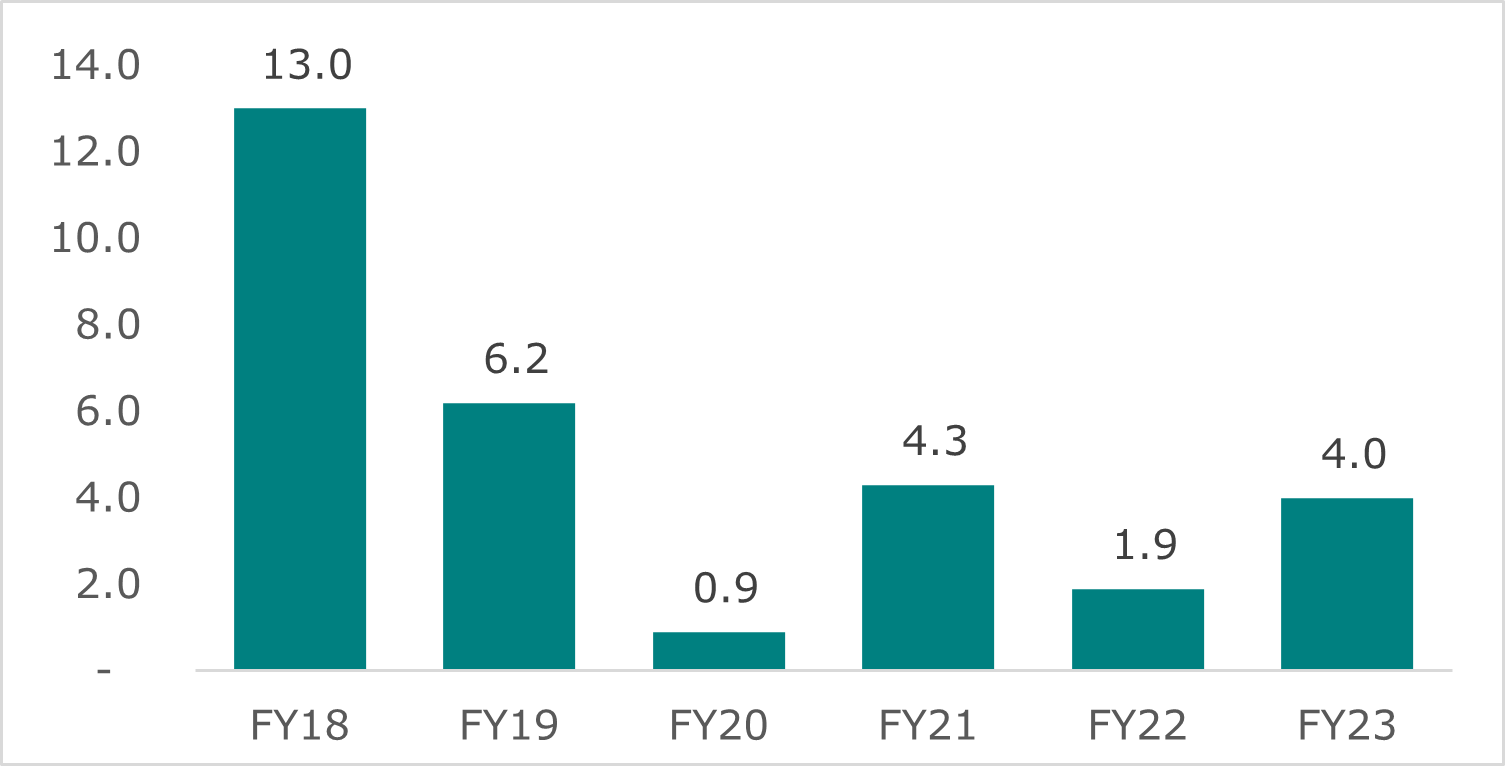